About Us
OUR STORY
Modular Plant Solutions (MPS) was born over a dinner conversation. Our co-founders were chatting about an opportunity to turn unusable stranded natural gas into a profitable commodity. That’s when the idea for MeOH-To-Go® (also known as Methanol-to-Go®), our small-scale methanol plant, was born. We wanted to figure out a way to convert the stranded natural gas into something transportable and profitable, even though the gas was in a remote location, not easily reachable nor near a pipeline.
That’s what led us to found MPS in 2016 and develop the design for MeOH-To-Go®, a small-scale, easily transportable, modular plant that uses stranded gas to produce market-ready, Grade AA methanol. We designed the plant modules with the patented idea that the frames are ISO-1496/CSC-container compliant, so they can be shipped via container ship, rail and truck, and reassembled quickly into a complete plant in the field.
Since then, we’ve expanded on our original design to allow for a variety of front-end feedstock options and process technologies, as well as back-end add-on technology processes, including Gasoline-To-Go® and DME-To-Go®. With each plant design, we also offer several options for low carbon intensity processes, resulting in methanol, gasoline and dimethyl ether with a lower CI score.
Our team of highly experienced engineers, operators and industry experts, bring the best-in-class plant solutions and hands-on experience for a variety of processes for the energy industry, including renewable energy, chemicals, oil & gas and petrochemical companies and more. Our team can modularize any plant design, with or without our patented module system.
OUR TEAM OF EXPERTS CAN HELP YOU PLAN, DESIGN, AND EXECUTE THE DEVELOPMENT OF YOUR MODULAR FACILITY, NO MATTER THE TYPE.
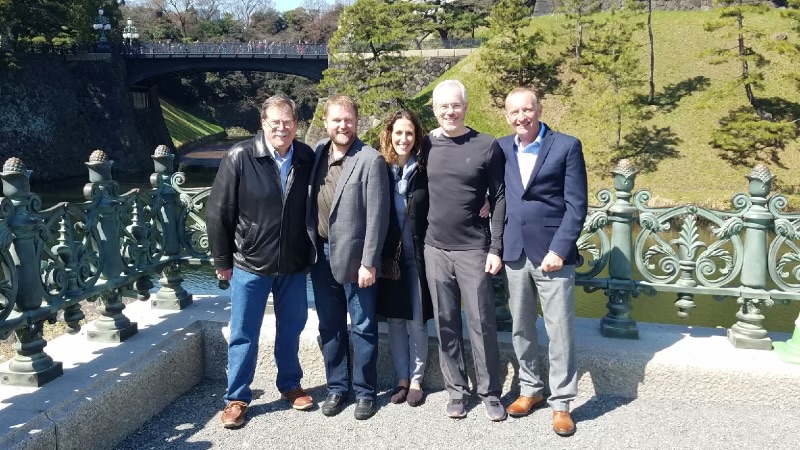
MPS VALUES
INTEGRITY
We hold ourselves and our work to the highest standards and principles.
PARTNERSHIP
We work with you to create a solution and plan that works best for all parties.
QUALITY
We provide world-class products and solutions.
DEPENDABILITY
We are good stewards of money, time, and talent.
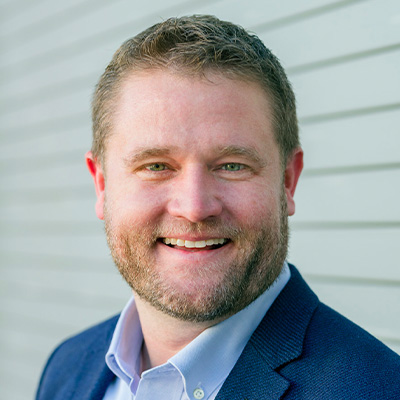
RUSSELL HILLENBERG
President and CEO, Co-Founder
Entrepreneurial Business from Baylor University
Russell’s specialty is business acumen, oversight and management. He is a third-generation family business owner. In 1967, his grandfather founded Woven Metal Products (WMP), of which he is now President. Russell has seen the growth of WMP over the years from that of a fabrication facility making custom metal parts, into the solutions provider of today, working with all major licensors in the oil and gas processing industry as well as end-users, refineries and chemical plants. Russell began as an Operator/Worker at WMP and worked through the ranks of Business Development, Field Superintendent, Administrative VP, and onto President. The WMP fabrication facility in Alvin, Texas, houses over 100,000 square feet of shop space, making it able to handle the fabrication needs of almost any size Reactor or Tower in the world. In 2016, Russell started Modular Plant Solutions with David Townsend.
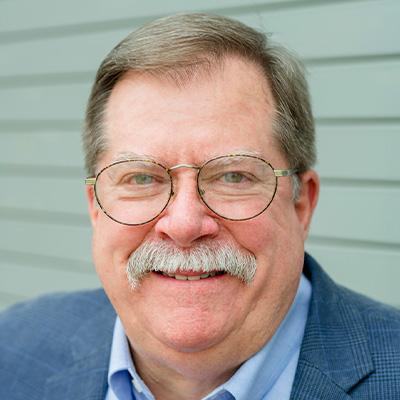
DAVID TOWNSEND, P.E.
VP of Engineering, Co-Founder
B.S. Chemical Engineering from Texas A&M, M.S. Chemistry from University of Houston Clear Lake
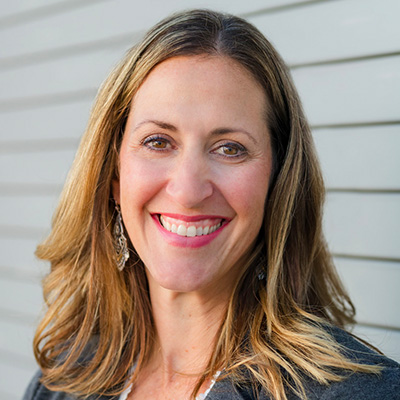
HEATHER BENNETT
VP, Business Development
B.S. from the University of Wyoming, MBA from University of Texas Dallas, MA International Management from University of Texas Dallas
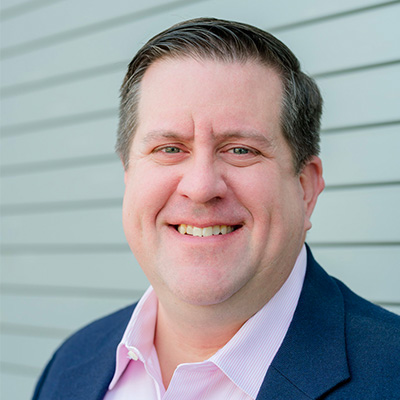
TONY HOPKINS
VP, Finance
B.B.A. from Lamar University, MBA from Rice University
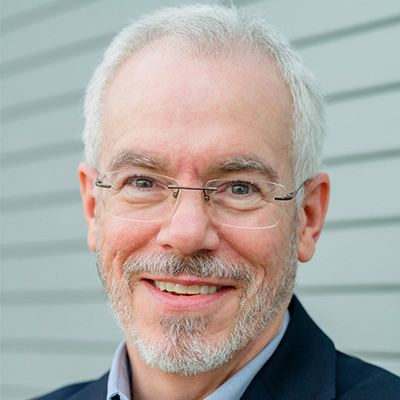
JOEL HENDRICKS
VP, Project Management
B.S Chemical Engineering from Washington University
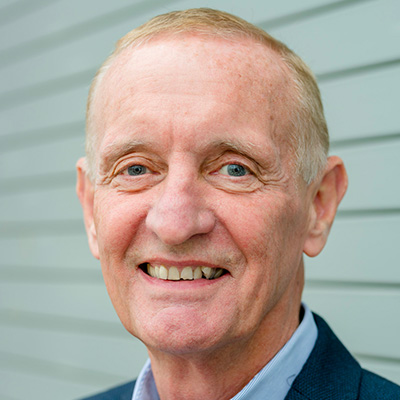
SID MOWBRAY
VP, Operations
National Diploma in Marine Engineering, Riverside College of Technology, Liverpool, England
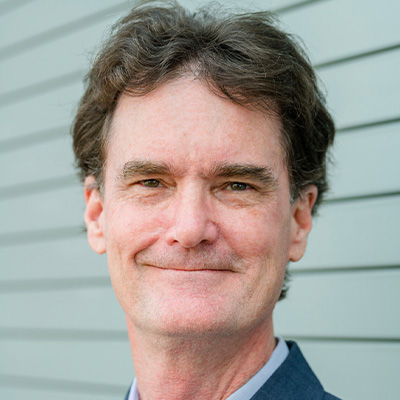
KNOX RIDER
Instrumentation Engineer
B.S. Electrical Engineering Texas A&M University
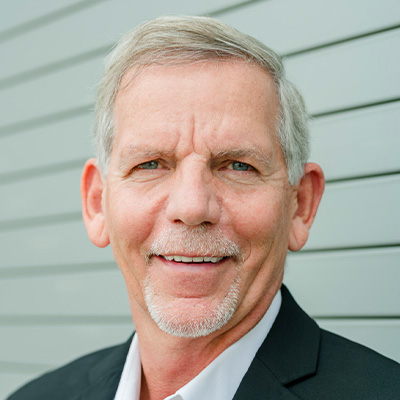
MARK PETERSON
Mechanical and Construction Engineer
B.S. Mechanical Engineering from Michigan State University
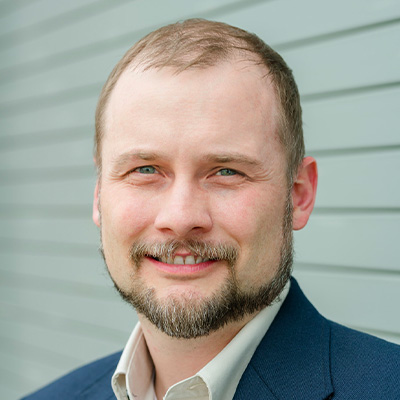
NATHAN NAGEL
Process Engineer
B.S. Chemistry from Texas A&M University
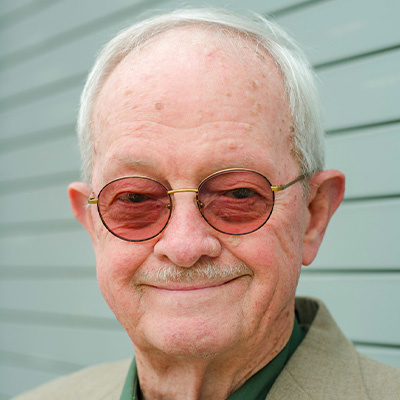
KEN FISCHER, P.E.
Rotating Equipment Engineer
B.S Mechanical Engineering from University of Houston
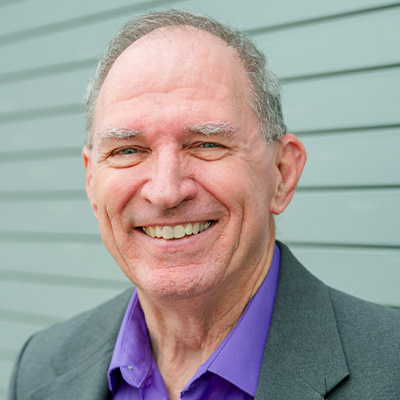
BOB BRYCE
Electrical Engineer
B.S. Electrical Engineering from Tennessee Tech
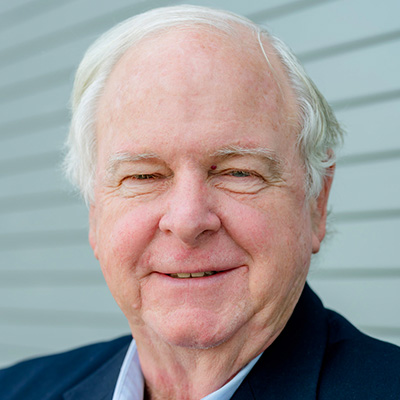
BOB THOMPSON, P.E.
Civil and Structural Engineer
B.S. in Civil Engineering Virginia Tech
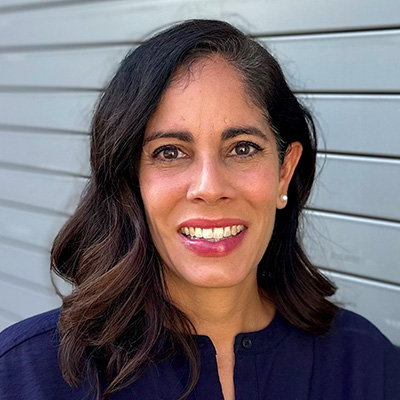
MONICA CERVANTES P.E.
Senior Electrical Engineer
B.S. and M.S. in Electrical Engineering from Texas A&M University
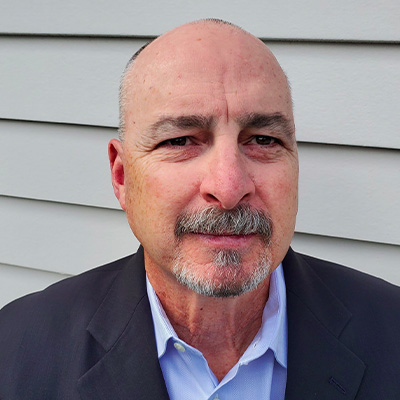
MARK MEDLEY
Technical Specialist
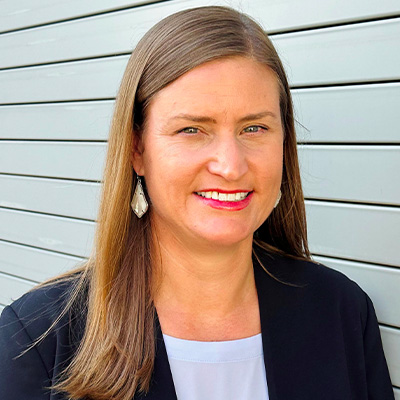
EMILY LOFTIN
Project Coordinator
B.B.A. and M.Ed. from the University of Oklahoma
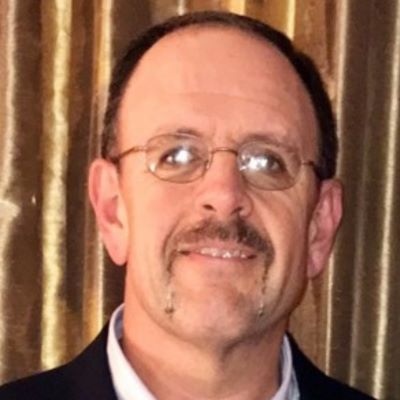
JIM BOB MITCHELL
Principal Consultant, Projects & Plant Operations
B.S. Biology from Tarleton State University
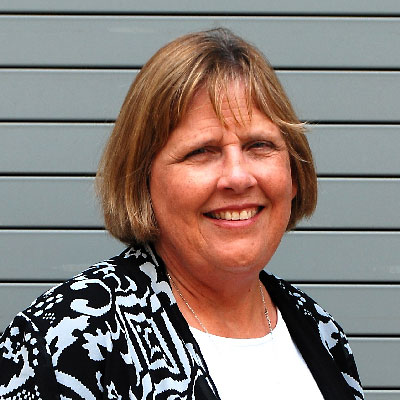
DELOME FAIR
Principal Process Engineer
M.S. Chemical Engineering from the University of Kansas
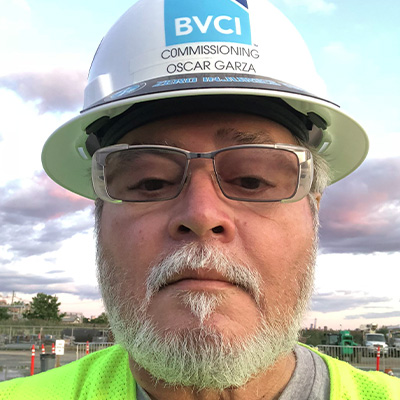
OSCAR GARZA
Commissioning and Startup Specialist
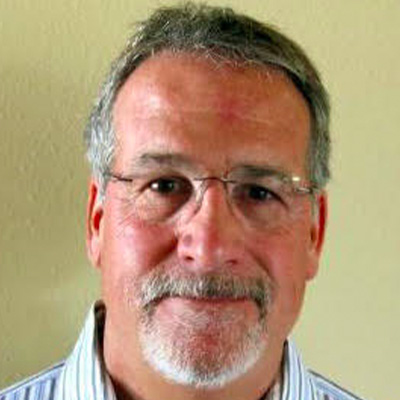
TOMMY DOGGETT
Commissioning, Startup, and Operations Manager
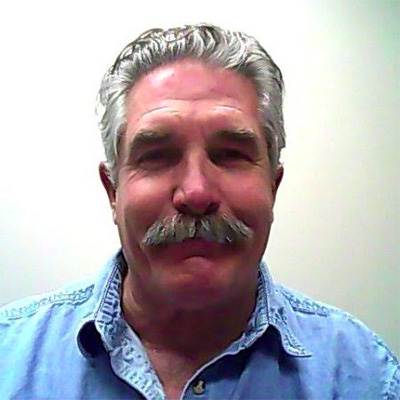
STEVE CLIFFORD
Commissioning and Startup Specialist
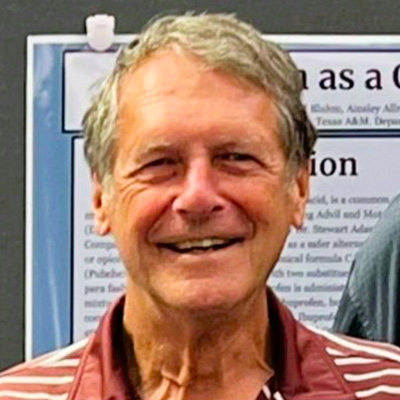
KEN WINDHORST
Industrial Chemist
B.S. Chemistry from Texas A&M, M.S. Chemistry from Texas A&M
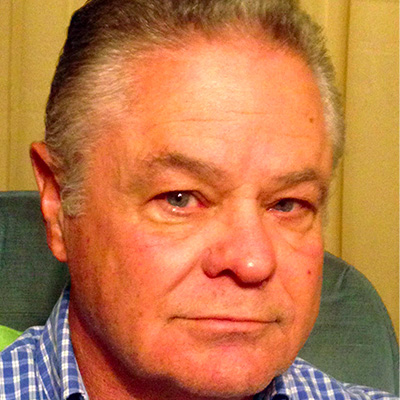
TERRY SANDERS
Rotating Equipment Specialist
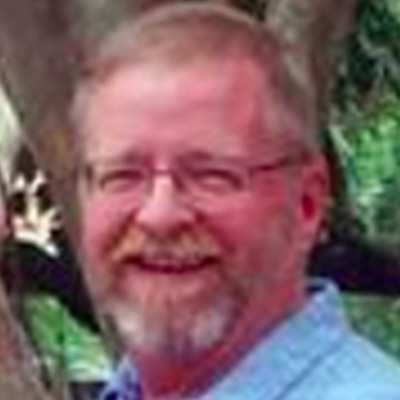
JIM CURTIS
Process Safety Engineer
B.S. & M.S. Chemical Engineering from Oklahoma State
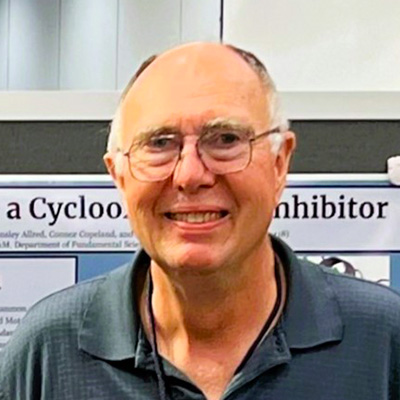
BOB LAMPTON
Environmental Engineer
B.S. Chemical Engineering from Texas A&M, MBA from University of Houston Clear Lake
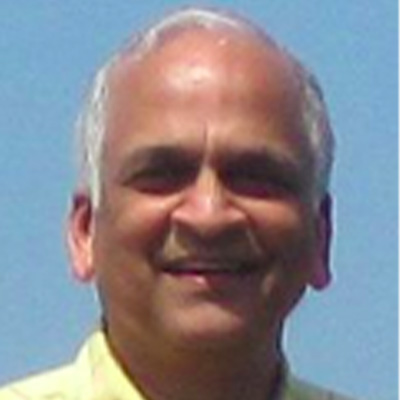
ASHOK RAKHE
Corrosion and Materials Engineer
B. Tech. Metallurgical Engineering, Indian Institute of Technology Bombay, M.S. Corrosion Engineering, The Ohio State University, Columbus